The Bill Young was a small silver mine above the townsite of Animas Forks. The mine never amounted to much, but it still has some interesting remnants.
The mine was located in 1873 and was developed by a 250’ deep shaft. Levels were driven at irregular intervals, with a total of around 1000’ of workings. It sat idle from the 1880s until 1935 when the shaft was dewatered. Maintenance work was done and the mine was made accessible to 200’. Apparently, the lowest level of the mine was never dewatered. From this later work, two small shipments of ore were produced in 1936.
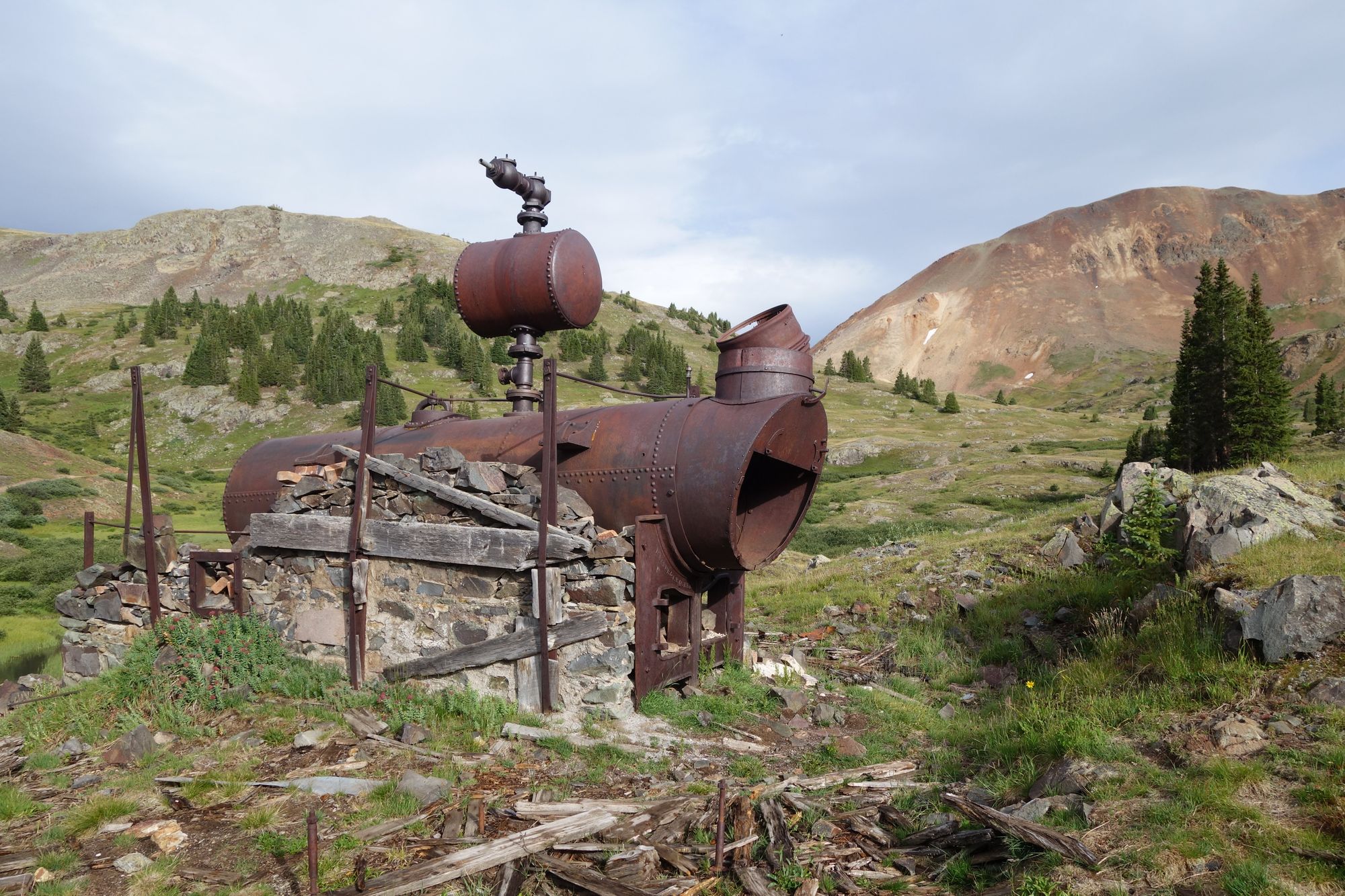
The site is fairly small, with a sealed shaft and some equipment next to it. It is on a large plateau and was lucky enough to have been spared the avalanches that tormented many of the mines in this mountain range. The boiler is an old Fraser & Chalmers, meaning it was produced before the 1901 merger that made the company Allis & Chalmers. An expansion tank for the steam sits above it precariously connected by a small pipe. Most of the rock placed around the boiler has fallen away, leaving it exposed. This rock would have been needed to insulate the boiler during operation.
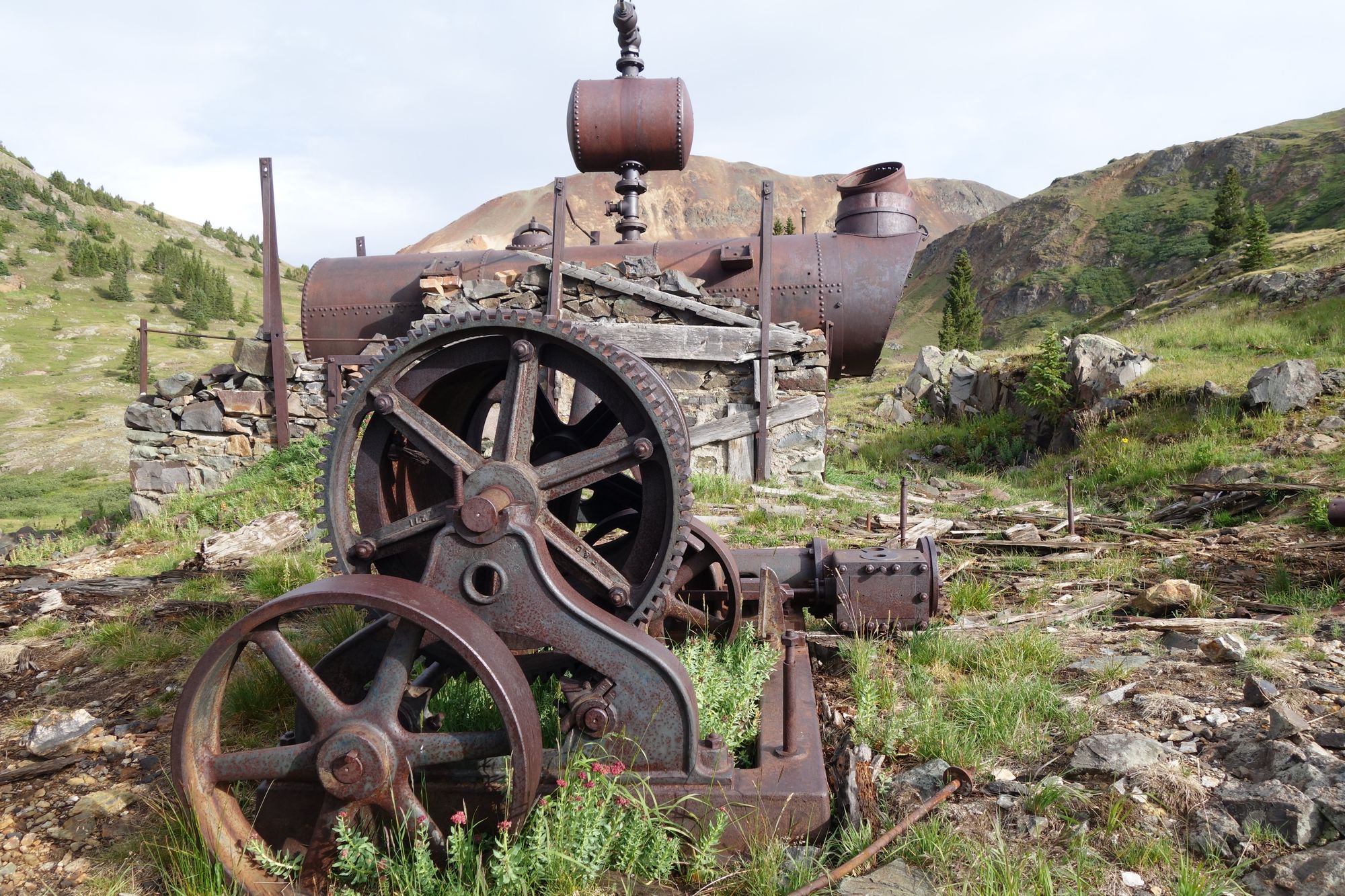
Next to the boiler is an elaborate small steam hoist. It was also made by Fraser & Chalmers and may have been part of a kit purchased by the mine. A small pulley was connected to one of the drive shafts which could have been belted to another piece of equipment if needed. The hoist is fairly modular, and it looks like no one piece would have weighed more than 300 lbs.
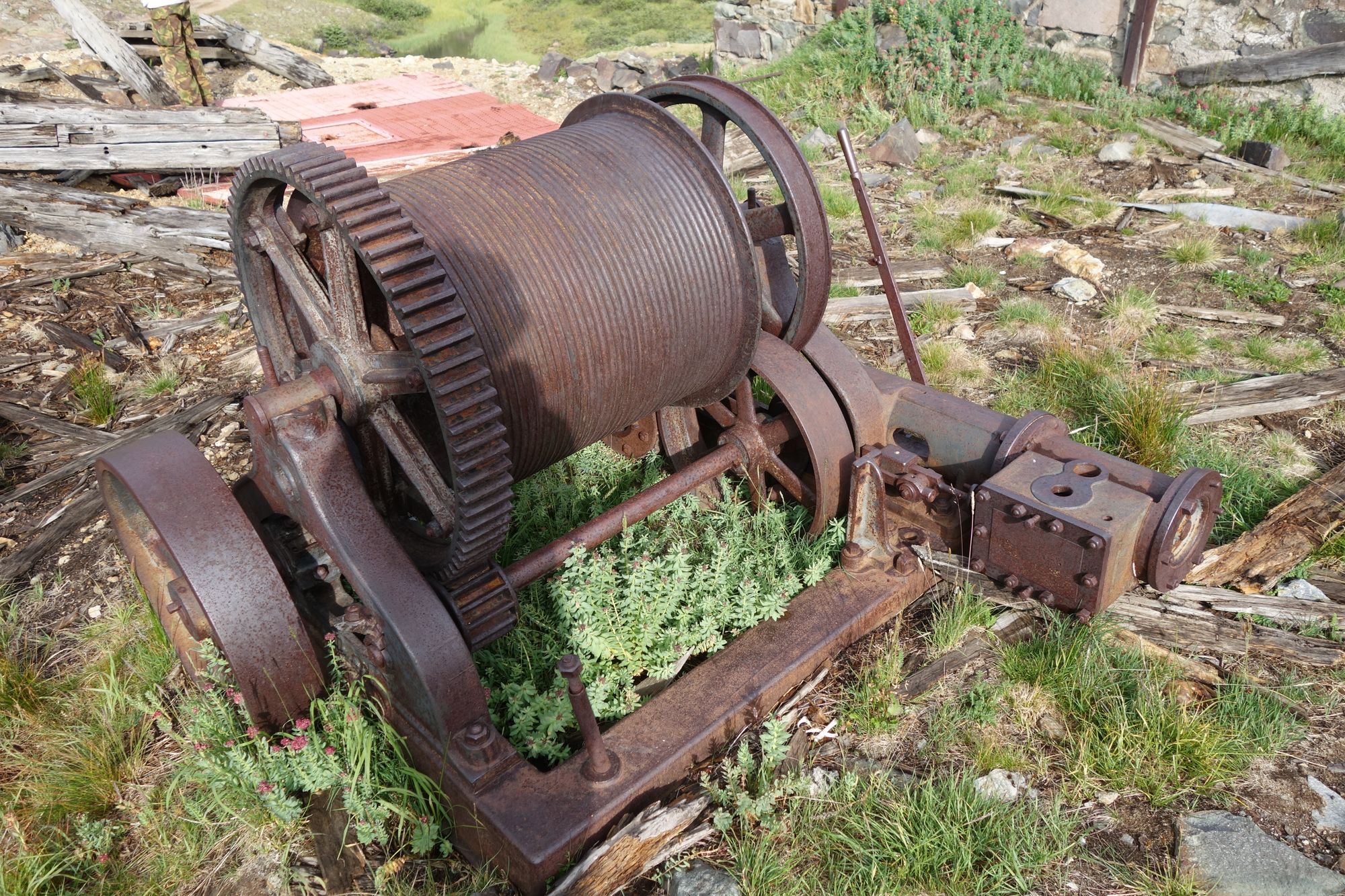
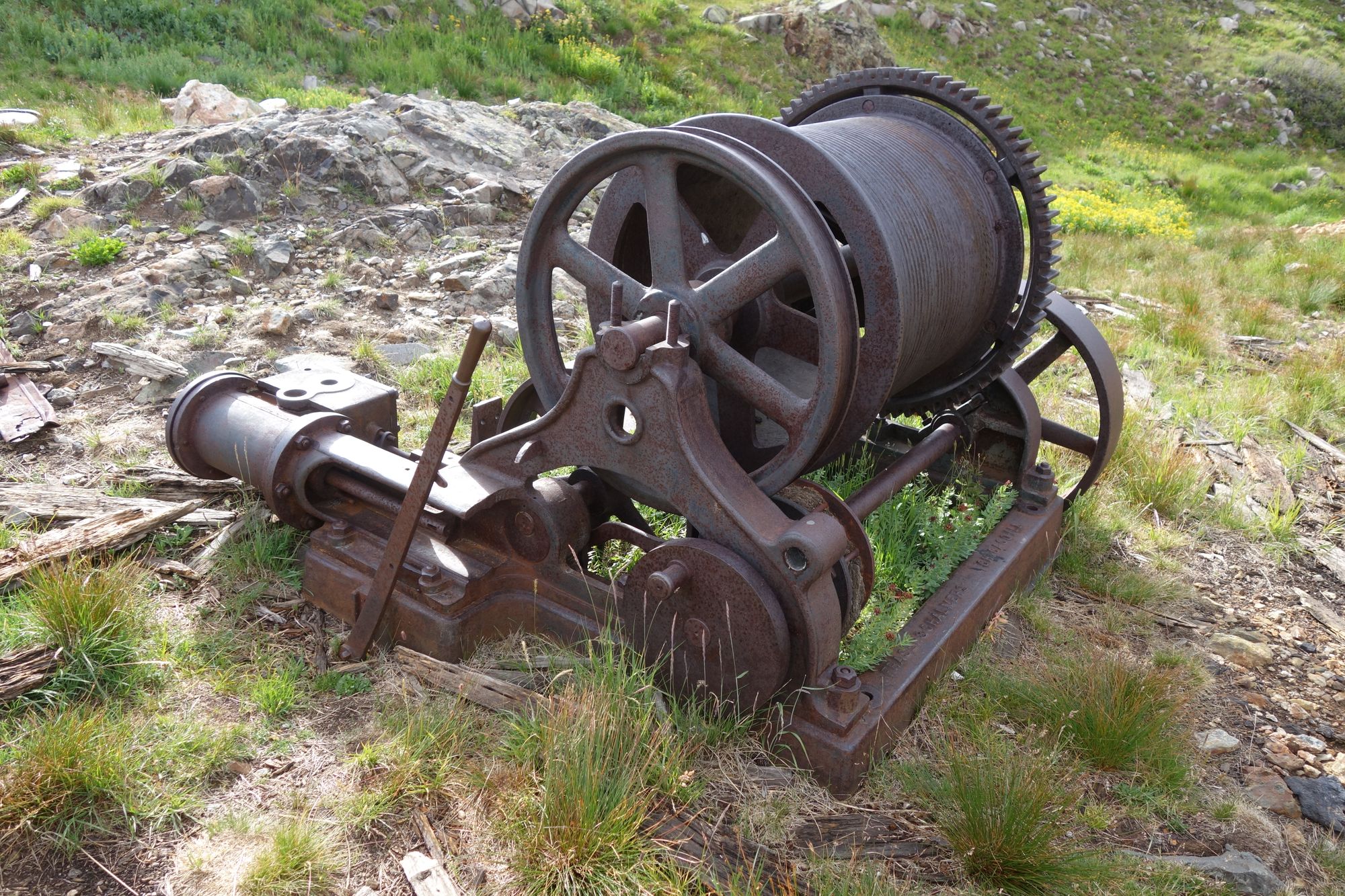
Hoist
The most unique feature about the hoist is its “geared-friction” drive. I’ll try to explain how this worked and why it was used. The machine was driven by a single slide valve steam engine that can be seen on one side. The steam engine would turn a leather roller, which would turn an iron wheel, which is connected to a gear, which spun the drum. The leather roller was tightly held against the iron one and they would interact with each other by friction. By having this friction connection, a sudden stoppage of the hoist would be less damaging to the machine as the wheels could slip. Generally, a steam hoist would just have gears, and if the bucket got caught in the shaft the sudden stopping of the drum could break gears. In a place as remote as this broken cast iron was something they truly wanted to avoid.
In practice, however, these friction drive hoists were frustrating to use as the wearing of the leather led the machine to slip more over time. If the leather wasn’t replaced in time, the hoist would be difficult to control and quite dangerous. A combination of gears and friction rollers shown here was designed to be the best of both worlds but never worked well. The friction rollers would still be something that could slip at undesirable times, but the addition of gears just gave the hoist something else to break.
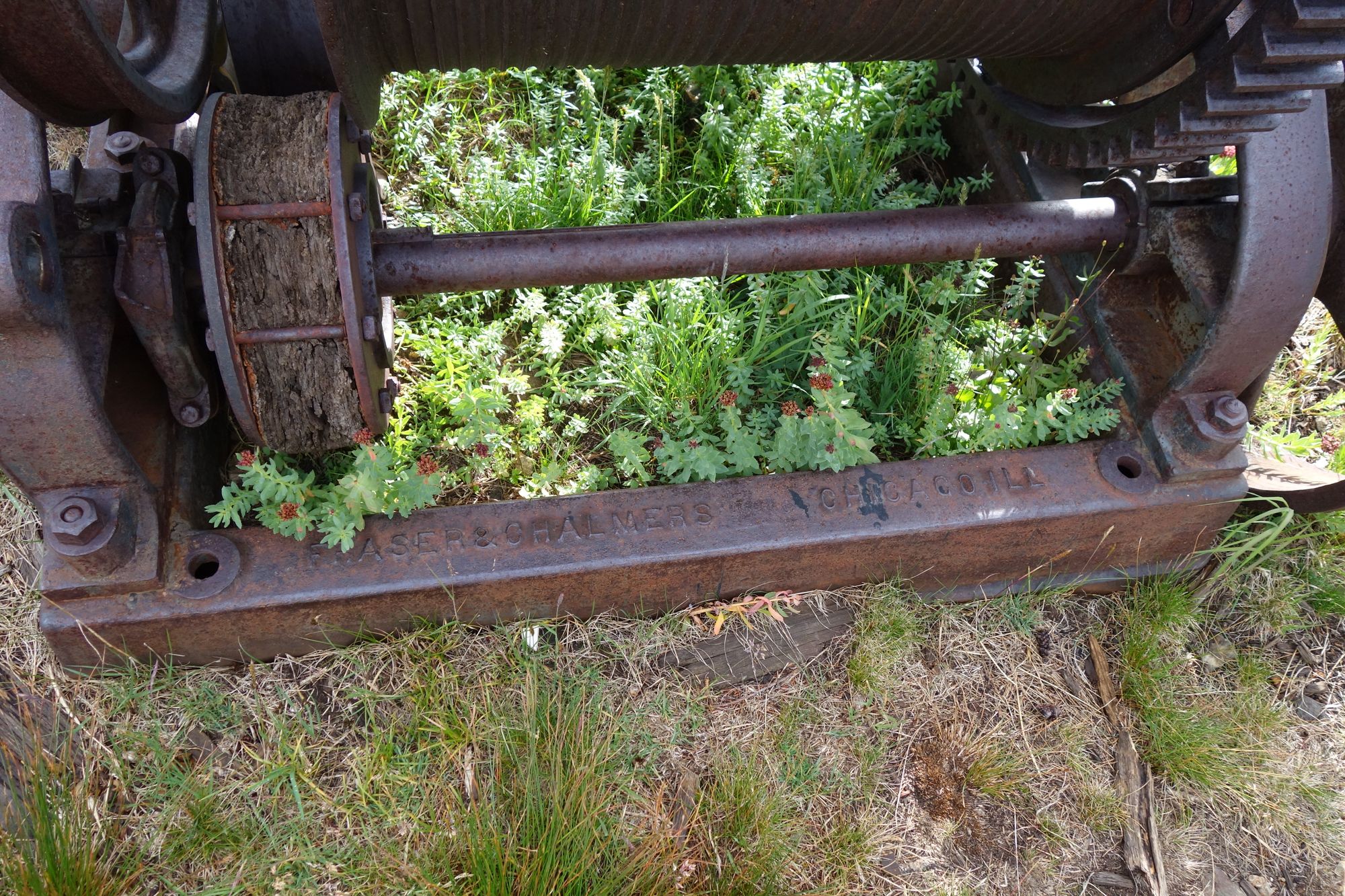